I ALWAYS THOUGHT that the diagrammatic representation of the “plan, do, check, act” cycle in ISO50001:2011 was a little strangely drawn (left-hand in picture below), although it does vaguely give the sense of a preparatory period followed by a repetitive cycle and occasional review. Turns out, though, that it was wrong all along because in the 2018 version of the Standard, the final draft of which is available to buy in advance of publication in August, it seems to have been “corrected” (right-hand below). For my money the new version is less meaningful than the old one.
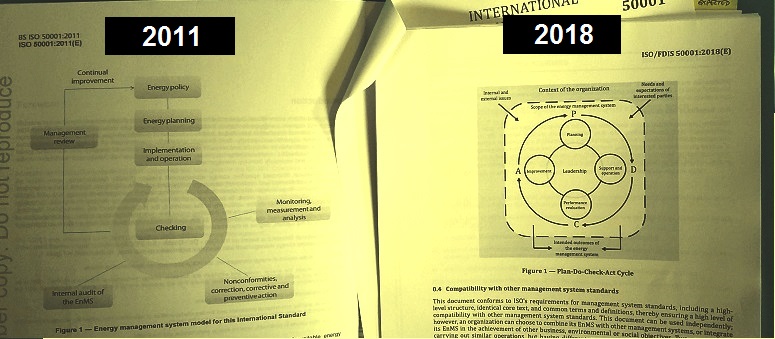
ISO50001 has been revised not because there was much fundamentally wrong with the 2011 version but as a matter of standards policy: it and other management-system standards such as ISO9001 (quality) and ISO14001 (environment) have a lot in common and are all being rewritten to match a new common “High Level Structure” with identical core text and harmonized definitions. ISO50001’s requirements, with one exception, will remain broadly the same as they were in 2011.
It is just a pity that ISO50001:2018 fails in some respects to meet its own stated objective of clarity, and there is evidence of muddled thinking on the part of the authors. The PDCA diagram is a case in point. I see also, for example, that the text refers to relevant variables (i.e., driving factors like degree days etc) affecting energy ‘performance’ whereas what they really affect is energy consumption. To take a trivial example, if you drive twice as many miles one week as another, your fuel consumption will be double but your fuel performance (expressed as miles per gallon) might well be the same. Mileage in this case is the relevant variable but it is the consumption, not the performance, that it affects. This wrong-headed view of ‘performance’ pervades the document and looking in the definitions section of the Standard you can see why: to most of us, energy performance means the effectiveness with which energy is converted into useful output or service; ISO50001:2018 however defines it as ‘measurable result(s) related to energy efficiency, energy use, and energy consumption’. I struggle to find practical meaning in that, and I suspect the drafting committee members themselves got confused by it.
Furthermore, the committee have ignored warnings about ambiguity in the way they use the term Energy Performance Indicator (EnPI). There are always two aspects to an EnPI: (a) the method by which it is calculated—what we might call the EnPI formulation—and (b) its numerical value at a given time. Where the new standard means the latter, it says so, and uses the phrase ‘EnPI value’ in such cases. However, when referring to the EnPI formulation, it unwisely expresses this merely as ‘EnPI’, which is open to misinterpretation by the unwary. For example Section 6.4, Energy Performance Indicators, says that the method for determining and updating the EnPI(s) shall be maintained as documented information. I bet a fair proportion of people will take the phrase ‘determining and updating the EnPI(s)’ to mean calculating their values. It does not. The absence of the word ‘values’ means that you should be determining and updating what EnPIs you use and how they are derived.
Failure to explicitly label EnPI ‘formulations’ as such has also led to an error in the text: section 9.1.1 bullet (a) (2) says that EnPIs need to be monitored and measured. That should obviously have said EnPI values.
The new version adds an explicit requirement to ‘demonstrate continual energy performance improvement’. No such explicit requirement appeared in the 2011 text, but since last year thanks to the rules governing certifying bodies, you cannot even be certified in the first place if you don’t meet this requirement. There was a lot of debate on this during consultation, but this new requirement survived even though it does not appear in the much-vaunted High Level Structure which ISO50001 was rewritten supposedly to conform to. That being the case, it is paramount that users adopt energy performance indicators that accurately reflect progress. Simple ratio-based metrics like kWh/tonne (or in data centres, Power Usage Effectiveness) are not fit for purpose and their users risk losing their certification because EnPIs of that kind often give perverse results and may fail to reflect savings that have really been achieved.
On a positive note, the new version of the Standard retains the requirement to compare actual and expected energy consumption, and to investigate significant deviations in energy performance. These requirements are actually central to effective ongoing energy management. Moreover, a proper understanding of how to calculate expected consumption is the key to the computation of accurate EnPIs, making it a mission-critical concept for anyone wanting to keep their certification.
This article is promoting my training courses on energy monitoring and targeting which include (a) the use of consumption data to detect hidden waste and (b) how to derive meaningful energy performance indicators.
This review is based on the Final Draft of ISO50001:2018 which has been released on sale prior to formal publication in August 2018.